Overall Equipment Effectiveness (OEE) measures a manufacturing process’s performance. Considering factors such as downtime, speed, and quality, OEE can provide a comprehensive view of process effectiveness.
Definition of overall equipment effectiveness
Overall Equipment Effectiveness (OEE) is a metric that can be used to measure the performance of manufacturing equipment. Three factors must be considered to calculate OEE: equipment availability, performance, and quality.
By considering these three factors, OEE provides a comprehensive view of manufacturing productivity.
Availability
The first factor to consider when calculating OEE is equipment availability. Equipment availability refers to the percentage of time that a piece of equipment can operate compared to the total amount of time it could be operated. For example, if a machine is available for 80% of the possible production time, its availability would be calculated as follows:
Availability = 80%
Performance
The second factor that goes into calculating OEE is equipment performance. Equipment performance takes into account the speed at which the equipment is able to operate as compared to its design speed. Design speed is the maximum rate at which a piece of equipment can operate without compromising quality or safety. To calculate performance, we use the following formula:
Performance = (Actual Output / Design Output) x 100%
For example, if a machine has a design output of 100 widgets per hour and it is actually able to produce 80 widgets per hour, its performance would be calculated as follows:
80 widgets per hour / 100 widgets per hour x 100% = 80%
100% Free Fundamentals of Lean COURSE
Quality
The third and final factor that goes into calculating OEE is quality. Quality refers to the number of good products produced compared to the total number of products produced. To calculate the quality, we use the following formula:
Quality = (Good Output / Total Output) x 100%
For example, if a machine produces 100 widgets and 90 of them are good, its quality would be calculated as follows: 90 widgets / 100 widgets x 100% = 90%
Overall equipment effectiveness calculation example
Now that we’ve gone over the three factors that go into calculating OEE, let’s put it together and see how it works in practice. Let’s say we have a machine that has an availability of 80%, a performance rating of 80%, and a quality rating of 90%. To calculate OEE, we would use the following formula:
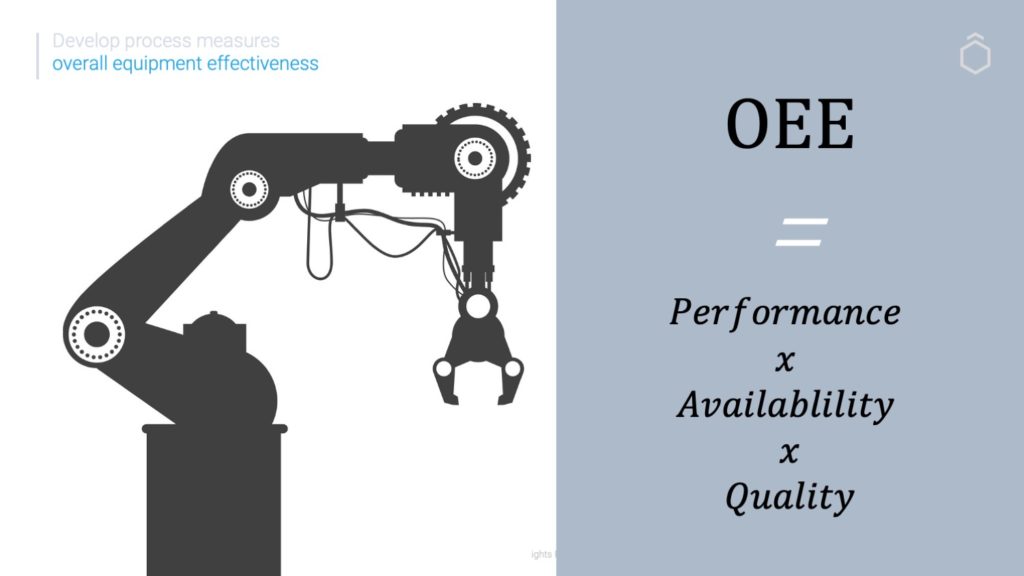
Overall equipment effectiveness formula
OEE = Availability x Performance x Quality
80% x 80% x 90% = 57.6%
In this case, our machine has an overall equipment effectiveness rating of 50.4%. This means that it can produce good products at its designed speed 50.4% of the time. While 50.4% may seem low, it is essential to remember that OEE is meant to be used as a benchmarking tool.
By comparing the OEE ratings of different machines or production lines, you can identify areas needing improvement and make changes accordingly. Additionally, minor improvements in any of the three factors can significantly impact the OEE rating.
For example, increasing availability from 80% to 85% would result in an OEE rating increase from 57.6% to 61.2%. As you can see, even small changes can significantly impact productivity!
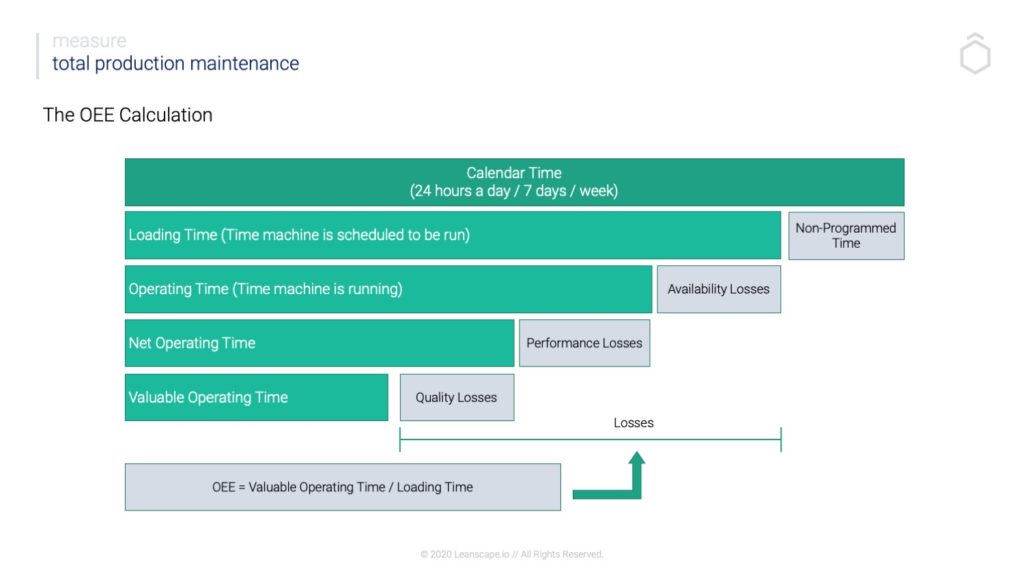