Understanding Takt Time: An Essential Guide for Business Improvement
In today’s fast-paced business world, companies strive to optimize their processes by becoming more efficient and achieving better productivity. One of the concepts that enable this optimization is Takt Time.
Takt Time, originally coined by the Japanese automotive industry, refers to the rate at which a product must be produced, or a task must be completed to meet the customer’s demand. Understanding Takt Time is crucial for businesses that want to streamline their processes, reduce waste, and increase profits. In this blog post, we’ll get into the details of what Takt Time is, how to define it, and its benefits in your business processes.
What is Takt Time? Takt Time Meaning
Takt Time, a concept central to lean manufacturing, refers to the rate at which a product needs to be produced to satisfy customer demand. The term “Takt” is derived from the German word “Taktzeit”, which translates to ‘cycle time‘. The calculation of Takt Time is crucial for businesses looking to optimise their production processes and eliminate waste.
Takt Time is calculated by dividing the total available production time by the customer demand. For instance, if a company has a total of 480 minutes available for production and needs to produce 240 units to meet customer demand, the Takt Time would be 2 minutes per unit. This calculation enables businesses to align their production rate with customer demand, thereby achieving higher efficiency and quality in their operations.
Ready to start your journey into the world of Lean with this free course?
FREE COURSE
A Lean focused continious improvement certification course
only £119
Propel your career forward, tackle complex problems and drive change
Only £167
How to Define Takt Time?
Defining Takt Time requires two pieces of information: customer demand and available production time. Customer demand refers to how many units must be produced within a specific time frame to meet the customers’ needs. Available production time is the total duration of production activities minus any planned downtime, such as setup, breaks, and maintenance.
Once you have this information, you can calculate Takt Time by dividing available production time by customer demand. Knowing your Takt Time is essential because it ensures that you produce Customer products at a rate that meets the customer’s demand.
Understanding Takt Time
Takt Time, a concept central to lean manufacturing, refers to the rate at which a product needs to be produced to satisfy customer demand. The term “Takt” is derived from the German word “Taktzeit”, which translates to ‘cycle time’. The calculation of Takt Time is crucial for businesses looking to optimise their production processes and eliminate waste.
Takt Time is calculated by dividing the total available production time by the customer demand. For instance, if a company has a total of 480 minutes available for production and needs to produce 240 units to meet customer demand, the Takt Time would be 2 minutes per unit. This calculation enables businesses to align their production rate with customer demand, thereby achieving higher efficiency and quality in their operations.
Takt Time Formula
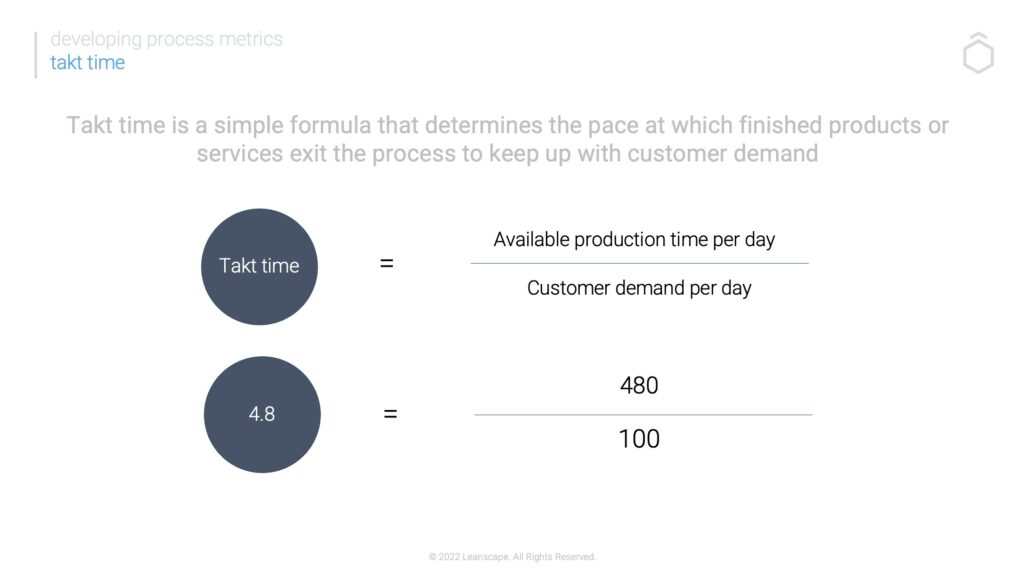
Benefits of Implementing Takt Time in Business Operations
Takt Time is a critical tool to align production with customer demand by setting a consistent pace for the production process. Calculating Takt Time establishes a standard that dictates how often a finished product should be completed to meet customer demand accurately. If a Takt Time of 2 minutes is established, for example, this means that a completed product should be coming off the production line every two minutes to meet the customer’s needs perfectly.
This synchronization not only ensures that the production rate meets demand but also aids in eliminating waste from overproduction and underutilization of resources. The balance provided by Takt Time reduces the likelihood of stockpiling or shortages, contributing to a more efficient, profitable, and customer-focused operation.
Challenges in Implementing Takt Time
Setting workstations based on Takt Time establishes a smooth and harmonious workflow. This is achieved by evenly distributing the workload across various workstations, each designed to complete a specific task within the determined Takt Time. Every workstation is aligned to produce at the same rate, ensuring a continuous production flow with minimal downtime or backlog.
For instance, if the Takt Time is two minutes, each workstation is tailored to complete its task within this time frame before passing it on to the next station. This synchronisation results in a production line that is highly coordinated and efficient, as each product progresses smoothly from one stage to the next without causing delays or bottlenecks.
Furthermore, by clearly understanding Takt Time, employees can work more systematically, reducing stress and increasing overall productivity. It also allows for quicker identification and resolution of any issues that may disrupt the workflow, thereby ensuring a consistent and high-quality output.
Demonstrating How Takt Time Prevents Overproduction: An Example
To illustrate how Takt Time prevents overproduction, consider this scenario: Imagine a toy manufacturing company ‘ToyJoy’ that has a demand to produce 600 toy cars a day. Their production line operates for 10 hours a day (600 minutes). By calculating the Takt Time, `600 minutes / 600 toy cars`, we find that the company needs to produce one toy car per minute to meet the demand without overproducing.
If ToyJoy disregards Takt Time and decides to produce at a faster rate, say one toy car every 30 seconds, they would end up with twice the demand, resulting in overproduction. This leads to excess inventory, increased storage costs, and a higher risk of waste due to potential unsold products.
By adhering to the Takt Time of one minute, ToyJoy can align their production with customer demand, producing just enough to meet the demand and thus, effectively preventing overproduction. This is an example of how Takt Time serves as a vital tool in lean manufacturing, helping businesses to improve efficiency and eliminate waste.
Integrating Takt Time into Your Business Strategy
Why it’s important managers understand and consider Takt Time
Understanding and considering Takt Time is essential for managers as it aids in achieving operational efficiency, maintaining product quality, and meeting customer expectations. With a clear comprehension of Takt Time, managers can strategically plan and control production processes, aligning them precisely with customer demand. This helps to avoid costly overproduction and waste of resources.
Moreover, understanding Takt Time also allows for the effective distribution of workload, resulting in a harmonious and stress-free work environment. By adhering to Takt Time, managers can ensure a smooth workflow, quickly identify bottlenecks or disruptions, and proactively address them, thus ensuring uninterrupted and efficient production.
Furthermore, a firm grasp of Takt Time equips managers with the ability to achieve balance in production, ensuring supply consistently meets demand. This balance is crucial for maintaining profitability and upholding customer satisfaction and trust in the business.
Tips for production teams to meet Takt Time goals (checklist, visual cues etc.)
- Use Visual Cues: Visual cues like charts, graphs, or timers can effectively communicate Takt Time to all team members. They provide a clear indication of the pace at which work should progress, helping maintain the set rate of production.
- Checklists: Implementing checklists can help ensure all tasks are performed within the Takt Time. They also allow for quick reference and ensure nothing is overlooked in the production process.
- Standardise Processes: Standardising work processes can help reduce variability and ensure consistency. This will make it easier to meet Takt Time goals as predictable and repeatable processes are more likely to stay within the set time limits.
- Training: Regular training can help team members understand the importance of Takt Time and how they can contribute to meeting it. It can also help identify areas of improvement in the current processes.
- Continuous Improvement: Practising continuous improvement can aid in constantly refining the process and making it more efficient over time, thereby helping to meet or even surpass Takt Time goals.
- Communication: Regular team meetings to discuss progress, issues, and suggestions can foster open communication and collaboration. This encourages problem-solving and helps maintain a steady workflow aligned with Takt Time.
- Balancing Workload: Distributing the workload evenly across all team members ensures that no single person is overburdened, which could potentially disrupt the Takt Time. Balancing workload also prevents bottlenecks that may slow down the process.
By implementing these practices, production teams can ensure a more efficient, well-aligned process that consistently meets Takt Time goals.
How Takt Time ultimately leads to higher customer satisfaction
Ultimately, Takt Time plays a pivotal role in enhancing customer satisfaction. By aligning production precisely with customer demand, it ensures that products are delivered on time, meeting the customers’ needs without delay. Moreover, as Takt Time aids in avoiding overproduction and underproduction, it contributes to a stable pricing structure, providing the customers with consistent and fair prices.
The standardisation and predictability of the production process, attributed to adhering to Takt Time, often result in superior product quality, enhancing the overall customer experience. Furthermore, the efficiency gained through observing Takt Time allows businesses to effectively manage their resources and potentially pass on cost savings to customers.
Lastly, Takt Time also facilitates swift and effective responses to market changes or shifts in customer demand, thus ensuring the business remains customer-centric. In essence, Takt Time provides a structured approach to meet the customer demand accurately, timely, and consistently, thereby leading to higher customer satisfaction.
Common myths about Takt Time that could cause confusion
Let us now debunk some common myths about Takt Time that could create confusion:
- Myth: Takt Time is fixed and cannot be changed. The reality is that Takt Time is a dynamic measure that is calculated based on customer demand. If demand changes, Takt Time should be recalculated and production adjusted accordingly.
- Myth: The reality is Takt Time is the same as cycle time. While they are related, they are not the same. Cycle time refers to the time it takes to complete a specific task or process, while Takt Time is the pace at which products need to be produced to meet customer demand.
- Myth: Takt Time only applies to production lines. In truth, Takt Time can be applied to any process where work is being done continuously, not just in manufacturing. It is a universal concept applicable to any operation seeking to align its output with customer demand.
- Myth: Lowering Takt Time always increases efficiency: Lowering itclearly understand can indeed increase production speed, but it does not necessarily mean higher efficiency. If Takt Time is set too low, it may cause overproduction, which leads to waste and increased costs.
By debunking these myths, we can clearly understand Takt Time and utilise it effectively in our operations for increased efficiency and customer satisfaction.
Real-life case studies of companies successfully implementing Takt Time
Toyota: Perhaps the most famous example is Toyota, the pioneer of the Lean manufacturing system where Takt Time is a fundamental element. By maintaining a steady production pace aligned with customer demand, Toyota has minimised waste and maximised efficiency, becoming a global leader in the automotive industry.
GE Appliances: This company significantly improved their production process by implementing Takt Time. By aligning their production rate with the customer demand, they reduced inventory and lead time, enhancing their market competitiveness.
Siemens Healthcare: Siemens applied Takt Time to streamline its diagnostic manufacturing process. As a result, they achieved a balanced workload across their production lines, improved throughput, and enhanced their ability to predict and meet delivery dates.
Boeing: Boeing uses Takt Time in its aircraft assembly lines to ensure a smooth and efficient production process. This has resulted in a reduction in the build time and cost while maintaining high-quality standards.
These examples illustrate the effectiveness of Takt Time in different industries and how its application can lead to substantial improvements in production efficiency and customer satisfaction.
Key takeaways on using Takt Time to maximize efficiency
In conclusion, Takt Time is crucial in lean manufacturing and operations, offering numerous benefits. Here are the key takeaways:
- Alignment with customer demand: Takt Time facilitates a seamless alignment between production rates and customer demand, preventing overproduction and underproduction.
- Efficiency and waste reduction: Adhering to Takt Time can optimise operational efficiency, reduce waste, and ultimately decrease costs.
- Predictability and planning: Takt Time provides a consistent production rhythm, enabling better planning and predictability.
- Flexibility: Takt Time isn’t rigid; it is adjustable based on changes in customer demand.
- Applicability: Takt Time principles can be applied across industries, not just in manufacturing.
- Customer satisfaction: By aligning production to customer demand, Takt Time can significantly enhance customer satisfaction.
Remember, the key to maximising efficiency using Takt Time is to continuously monitor customer demand, adjust production accordingly, and consistently seek ways to refine your processes.
Takt Time Conclusion
In wrapping up, Takt Time emerges as a powerful tool within Lean Manufacturing and operations management, providing a systematic and customer-centric approach to production.
As we have seen, the dynamic nature of Takt Time allows it to be finely tuned to match customer demand, promoting efficiency and reducing waste. More than just a production guideline, Takt Time is a strategic asset that aids in better planning and predictability, offering an edge in an increasingly competitive market landscape. Its principles possess universal applicability, extending beyond the confines of manufacturing to various sectors and industries.
Importantly, the customer satisfaction achieved through Takt Time’s implementation is a testament to its effectiveness. Customers receive timely, quality products by ensuring a steady, demand-matched production flow, enhancing their overall experience and relationship with the company. Thus, Takt Time is a testament to the value of aligning business operations to customer needs, which is a critical factor in boosting efficiency, competitiveness, and customer satisfaction.